Lexmark Blog
Thought Leadership
Data-led business transformation: Applying data intelligence to manufacturing
| By Michael Bensing, Senior Toner Development Engineer, Lexmark
With the power of democratised data and analysis, Lexmark increased efficiency and decreased operating costs in the manufacturing of our proprietary toner.
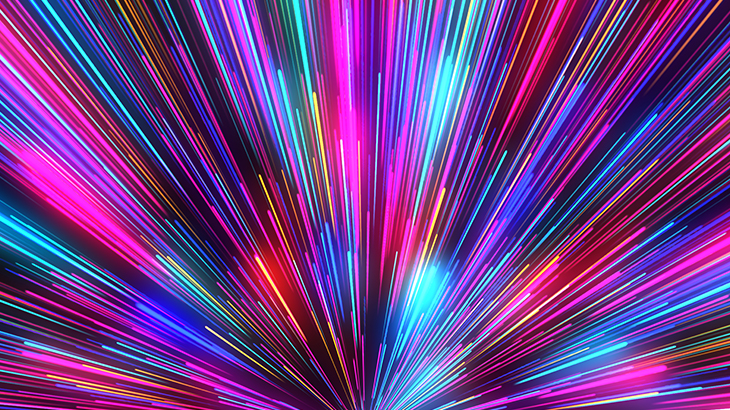
TAGS: Internet of Things , Artificial Intelligence, Manufacturing, Thought Leadership, Analytics, Digital Thread
Despite the clear business value of data and analytics, only 14% of enterprises today make them broadly accessible to employees. And just 52% of frontline employees have access to these insights for their daily work. When data is free flowing, insights can be extracted and used to address challenges across the business.
Leaders are noticing these benefits and acting to make data more readily available, as we did at Lexmark. To speed up our digital transformation journey and make our data more actionable, we broke down internal silos, empowered employees to analyse and reshare insights, and embraced organisational change.
With the power of data at our fingertips, we pushed ourselves to find areas of our business we could further improve with data analysis. One clear opportunity: our manufacturing efficiency and operating costs.
Using analytics to improve complex processes
One area where we applied analytics is for the toner we manufacture for our printers. Developing toner is a complex, multi-step chemical process overseen by our team members. The process itself is an attempt to destabilise materials in a controlled manner. It’s a difficult, delicate process that can be thrown off by even a minor variation.
Because of the nature of human decision making – with differing opinions and judgements – the process wasn’t always precise. Compounding the situation, the human decisions were made with limited, real-time insights, and they didn’t tap into the full breadth of our analytics capabilities. As a result, we often saw a wide range of outcomes, from uncontrollable particle growth to long, inconsistent cycle times.
To address this, we embarked on a data-driven exploration to improve process control and reduce cycle times. Our first step was to leverage the power of the vast amounts of data we create.
Data as a solution
Our manufacturing system generates and saves large amounts of data from each batch of toner. Yet, we were not actively analysing and extracting insights from it. This oversight and lack of knowledge sharing was the first thing we looked to address.
To start, we combined, cleaned and analysed historical manufacturing data sets. An estimated 20 million data points from 200 toner batches informed our analysis.
Through this research, we found the source of our process control issues. Unbeknownst to us, one minor element had a huge impact on outcomes. Armed with this new knowledge, we were able to adjust our approach and build more accurate algorithms to drive decisions for consistent outcomes.
Cultivating a culture of innovation
This and other discoveries — and their resulting improvements — were only made possible because of the efforts of one of our team members, Catherine Randolph. Formerly an R&D scientist at Lexmark, Randolph joined the toner development team, empowered to follow her passion for data analysis with this project.
She and other Lexmark team members reviewed scientific literature to better understand the toner manufacturing process and how it could be improved. While there’s a lot of research on manufacturing, the process models described were typically based on simpler systems and none directly focused on the process for toner. Randolph’s particular interest in a data-driven approach, plus our need to address process control, created the perfect environment for her to develop and drive this project.
Data-driven results
With the new data-driven model for toner production in place, we have made notable improvements in process control, significantly reduced overall cycle time and slashed our manufacturing expenses. Our efforts won a Manufacturing Leadership Award for outstanding achievement in engineering and production technology.
This project will continue in phases, and we expect to see an even greater improvement across the board when finished. This process showed us how powerful data can be and the importance of not letting any insights go to waste.
Throughout this process, we discovered three key findings that you can apply to your business:
- Success itself is a lesson. Look for ways to take the processes and insights you’ve learnt from in one area and apply them to other parts of your business for greatest impact.
- Be realistic about your needs – including resources and timeline – and dedicate the proper amount of each to it. You’ll see better results when you do something the right way the first time.
- You can never predict where innovation will come from. One idea can change your entire business – that’s one reason cultivating a culture of innovation is so important. Though a passion project might only be a minority of team members’ time, it has the potential for significant efficiency gains.
Are you ready to harness the transformative power of your data?